As a 3D printing enthusiast who’s witnessed the evolution of 3D printing over the past 5 years, I’ve seen this technology transform from a prototyping tool into a viable option for mass production. Today, I’ll dive deep into how 3D printing is reshaping manufacturing landscapes and explore its potential for large-scale production.
The Current State of 3D Printing in Manufacturing
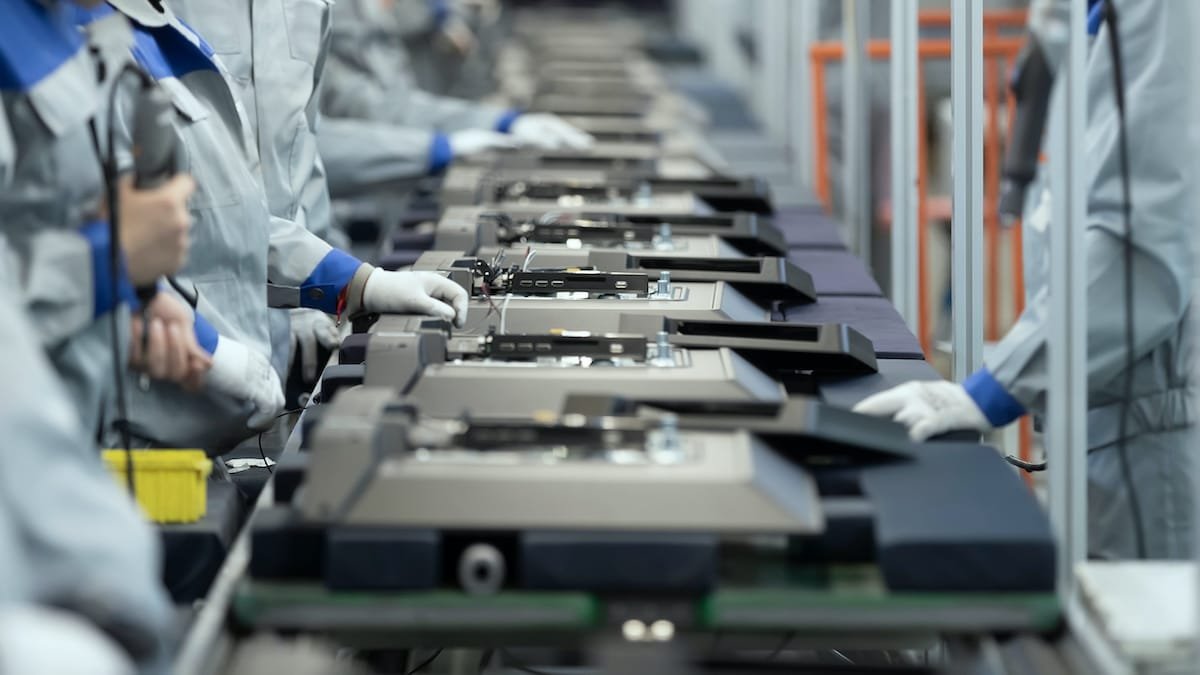
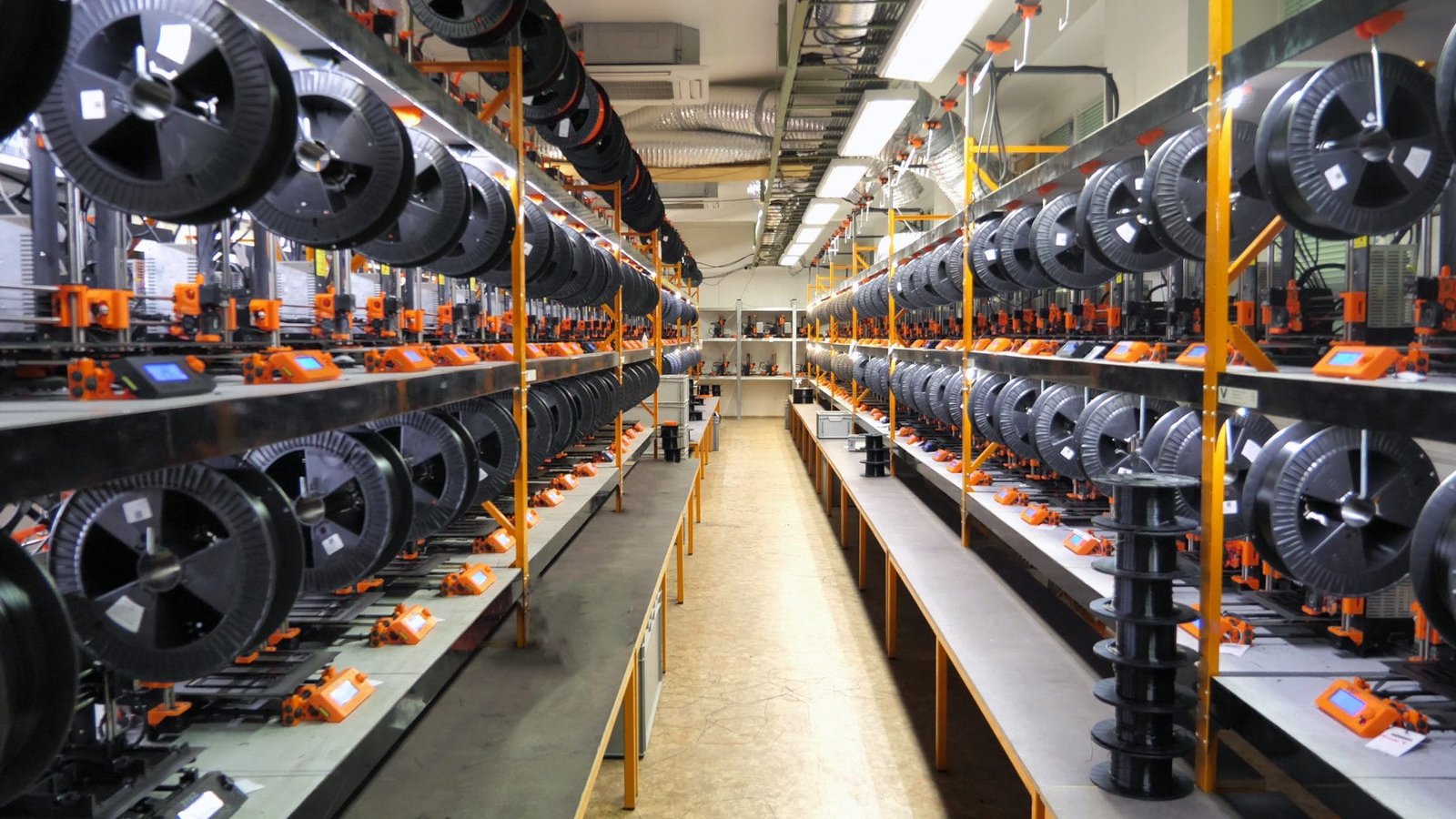
The days when 3D printing was solely used for prototyping are behind us. Major companies like Adidas, GE Aviation, and Airbus are now incorporating 3D printing into their mass production processes. While it hasn’t completely revolutionized manufacturing as some predicted, it has carved out its own significant niche in the production ecosystem.
Success Stories: Companies Leading the Way
Several industry leaders have successfully implemented 3D printing for mass production, with impressive results:
- Adidas: Through their partnership with Carbon, they’ve produced over 4 million pairs of 4D midsoles as of 2022. Their 4D technology allows for custom-designed midsoles that optimize athletic performance. The company aims to scale this to tens of millions of pairs annually.1
- GE Aviation: Has manufactured over 100,000 fuel nozzles using 3D printing since 2015. These nozzles are 25% lighter and five times more durable than traditionally manufactured versions. The LEAP engine, which uses these nozzles, has accumulated orders worth more than $140 billion.2
- Airbus: By 2021, had installed over 1,000 3D-printed parts across their A350 XWB aircraft fleet. One notable example is their titanium bracket, which reduced weight by 40% compared to traditional manufacturing methods. Airbus produces approximately 2,700 3D-printed parts monthly.3
- IKEA: Launched their FLAMTRÄD collection in 2022, producing thousands of 3D-printed home accessories monthly. Their wall hangers and decorative items demonstrate how 3D printing can be applied to consumer goods at scale.4
- Hearing Aid Industry: Perhaps the most comprehensive adoption of 3D printing for mass production – over 90% of custom hearing aid shells worldwide are now 3D printed, representing approximately 15 million units annually. This transformation happened in less than 500 days, demonstrating one of the fastest industrial adoptions of 3D printing.5
Advantages That Make Mass Production Viable
I’ve identified several key benefits that make 3D printing attractive for mass production:
- Supply Chain Flexibility
- Distributed manufacturing capabilities
- Reduced dependency on global supply chains
- On-demand production potential
- Design Freedom
- Complex geometries impossible with traditional methods
- Internal features and structures
- Part consolidation opportunities
- Cost Effectiveness
- No minimum order quantities
- Reduced inventory costs
- Lower tooling expenses
Limitations and Challenges
Despite its potential, several factors still limit widespread adoption:
Challenge | Impact | Potential Solutions |
---|---|---|
Speed | Slower than traditional methods | Advanced printer technology, multiple printer farms |
Cost | High initial investment | Leasing options, gradual scaling |
Materials | Limited compared to traditional manufacturing | Ongoing research and development |
Size constraints | Build volume limitations | Modular designs, strategic part splitting |
When Does 3D Printing Make Sense for Mass Production?
Based on my experience, 3D printing is most effective for mass production in these scenarios:
- Complex geometries that are difficult to manufacture traditionally
- Customized products requiring frequent variations
- Medium-volume production runs (1,000-100,000 units)
- Products with consolidated parts that reduce assembly time
- Lightweight components where material savings justify costs
Technology and Material Considerations
1. FDM (Fused Deposition Modeling)
- Reliability: 95-98% success rate in industrial settings
- Material Cost: €35-45 per kg for industrial-grade filaments
- Speed: Typical production rate of 164-246 cm³ per hour
Notable Examples:
- Consumer Products: Prusa Research produces 100,000+ 3D printer parts monthly
- 500+ printers running 24/7
- Less than 1% waste rate
- Materials: PETG, ASA, and PC Blend
2. SLS (Selective Laser Sintering)
- Build Speed: Up to 1.8L per hour on advanced systems
- Material Cost: €45-90 per kg for production-grade powders
- Part Accuracy: ±0.1mm per 100mm
Real Production Examples:

- Boeing Satellite Components:
- 300+ unique parts per satellite
- 50% weight reduction
- Material: PA12 (Nylon) with aluminum-filled variants
- Medical Devices (Clear Dental Aligners):
- Production volume: 500,000+ aligners daily worldwide
- Material: Tera Harz TC-85
- Accuracy: 50 microns layer resolution
3. Metal Printing (DMLS/SLM)
- Build Speed: 15-120 cm³ per hour
- Material Cost: €315-450 per kg for metal powders
- Energy Usage: 0.5-1.0 kWh per cm³
Production Examples:
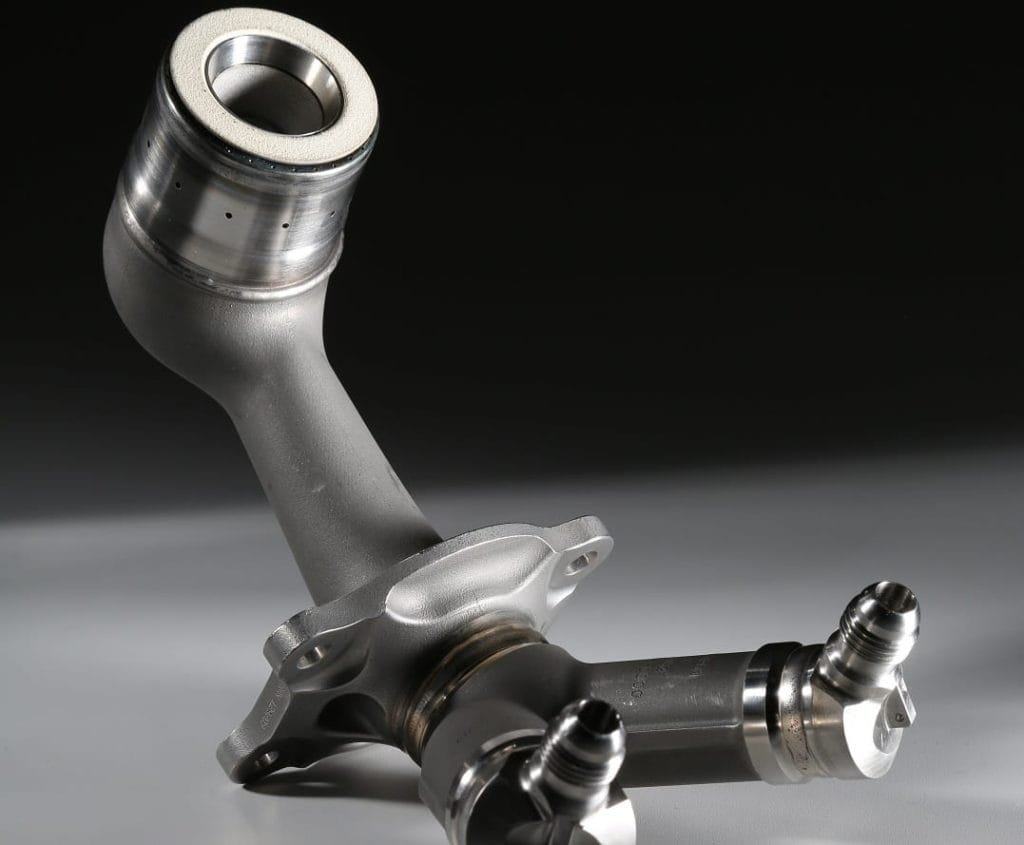
- GE LEAP Engine Fuel Nozzle:
- Annual Production: 100,000+ units
- Consolidates 20 parts into one
- Material: Cobalt-chrome alloy
- 25% weight reduction
- Five times more durable than conventional nozzles
- Stryker Medical Implants:
- Over 2 million implants produced
- Material: Ti6Al4V (Titanium alloy)
- 66% more porous structure than traditional implants
- FDA-approved for mass production
Future Outlook and Innovations
The future of 3D printing in mass production looks promising, with several developments on the horizon:
- Faster printing speeds through new technologies
- Expanded material options
- Improved automation and quality control
- Integration with Industry 4.0 principles
- Enhanced software for production management
Key Takeaways
- 3D printing is viable for mass production in specific applications and industries
- Success depends on choosing the right applications and understanding limitations
- The technology offers unique advantages in customization and complex geometries
- Cost-effectiveness improves with higher complexity and lower volume requirements
- Future innovations will expand mass production capabilities
As I conclude, it’s clear that while 3D printing won’t replace all traditional manufacturing methods, it has established itself as a valuable tool in the mass production toolkit. The key to success lies in understanding where and how to apply this technology effectively.
The question isn’t whether 3D printing can be used for mass production—it already is. The real question is how to best leverage its strengths for your specific manufacturing needs. As technology continues to advance and costs decrease, we’ll likely see even more applications where 3D printing becomes the preferred method for mass production.